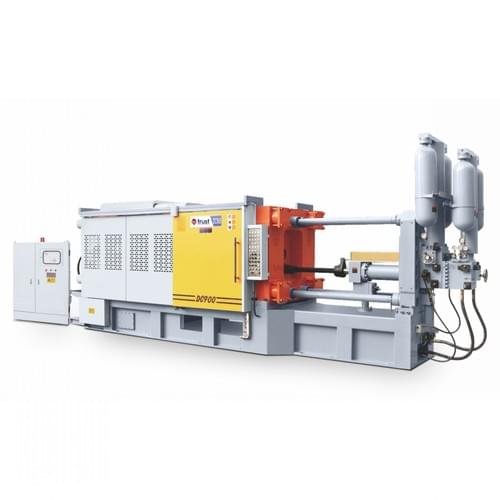
Servo motor power saving 2000Ton aluminum alloy high pressure die casting machine
Model:DC2000
Clamping force:20000KN
More info please contact us.
Servo motor power saving 2000Ton aluminum alloy high pressure die casting machine
Features
1. The mold platen material is made of nodular cast iron and special alloy material. with good ductility and can better absorb the impact force of injection; High surface hardness, effectively reduce the die extrusion and impact marks. The formwork adopts thickened design to ensure that the formwork surface is not easy to sag and fracture during long-term use.
2. The movable mold platen adopts the rib plate structure design, which not only enhances the strength of the middle plate from the structure, but also solves a series of problems existing in the suspended thimble structure commonly used in the industry.
3. All moving joints of the machine shall be provided with alloy steel bush, and with liquid nitrogen cold charging process, the joint pressure shall be uniform, so as to effectively extend the service life of the machine.
4. According to the design standard of imported machine, medium frequency processing is adopted for the thread of tie-bar, which improves the hardness and wear resistance of the thread pair, and solves the common problems of mold adjustment and thread strain in the industry.
5. The machine base adopts integral I-shaped steel structure and adds steel beam support structure. Combined with heat treatment process, it has better rigidity and is not easy to deform, effectively maintaining the accuracy of long-term use of the machine.
6. The special alloy material and heat treatment process are adopted for the tie-bar, and the vertical and horizontal two-way stress release system is added to ensure the stable clamping force of the whole machine and prolong the service life of the tie-bar.
7. High performance injection system, with active injection and direct pressurization structure, equipped with high-performance energy storage system, optimizes the oil circuit of the injection system, reduces the loss in the process of energy transfer, the injection acceleration reaches 60g, and greatly improves the stability and repeatability of key parameters. In addition, the injection system is equipped with automatic energy storage function, automatic calculation and matching function of energy storage pressure, pressurization failure alarm function, nitrogen leakage alarm function, automatic unloading function, etc.
8. Cartridge valve opening adjustment mechanism, self-developed cartridge valve opening adjustment mechanism, solved the technical problems of adjustment difficulty in the industry.
9. The appearance design led by the world's leading industrial design team has provided innovative design for nearly 2000 customers around the world, with grand and practical appearance.
Highlights
PLC Control System
The PLC adopts Omron / Siemens color display touch screen and artificial intelligence operation control.
Injection System
The well designed injection control system, with the parameters adjustable, is suitable for the production of various high precision products.
Clamping System
- High strength toggle structure design ensures more stable and durable machine base.
- The thickness and toggle are strengthened, and the guide sleeve of the middle plate is lengthened by 30%, which ensures the high stability and balance of the mold platen operation.
Hydraulic Control System
Double proportional control oil circuit, pressure and speed can be adjusted automatically.
Cut off the design of oil circuit to ensure the stable operation of hydraulic system.
Ejection System
High strength mechanical structure, double ejector cylinder(≥300Ton).
Lubrication System
Central automatic lubrication system, timing lubrication toggle, improve mechanical life and reduce maintenance.
General technology
Servo Motor Energy Saving System /Oil Cooling System(option)
- High efficiency and excellence in energy saving
The die casting machine automatically adjusts the flow pressure based on the computer setting. The overall energy saving effect can reach 45%~75%.
- Low noise
Noise during normal operation less than 65dB, to achieve quiet operation and improve the working environment.
- High speed response
The overall system dynamic response time is less than 50ms, and the production efficiency is increased by 5% to 7% over the ordinary models.
- High-precision control
The PID adjustment of the system flow and pressure by the oil-cooled servo driver makes that the repeatable precision of the entire oil system is controlled within 0.3% to ensure product quality.
- Increase of service life
The double closed loop of flow pressure makes the machine run steadily and with high repeatability, greatly reducing the strike, relieving the wear of various components and prolonging the service life.
Real Time Closed Loop Injection Control System (option)
Injection with real time adjustments of key parameters to ensure highest process stability and precision.
- Constant acceleration of 1st Phase velocity
Optimized 1st phase to minimize or avoid air entrapment during pre-filling. - Precise and quick switch to fast filling phase
Precise switch to fast filling to achieve the ideal injection process. - Fast and precise switch-over to intensification phase
Quick and precise trigger of intensification phase to allow quick pressure build up time. - Speed brake at the end of cavity filling
Braking in high speed injection, not only reduces flash build up but also increase die service life.